Rising labor costs abroad, abundant energy supplies at home, direct foreign investment, and increasing U.S. demand are all powering America’s manufacturing renaissance. What’s less understood, however, is the importance of available metals and minerals, materials that are used to make everything from cell phones and laptops to body armor, medical devices, and machinery.
Industry leaders know what they need, of course, and have been busy educating policymakers. Last July, for example, representatives from GE Global Research (Niskayuna, NY) testified at a U.S. House subcommittee hearing about America’s metal and mineral security. Over 91% of executives are concerned about supply disruptions beyond their control, and potential shortages of critical materials are of special concern.
As Hal Quinn of the National Mining Association (NMA) and Harry Moser of the Reshoring Initiative explain, these worries are well-founded. According to the United States Geological Survey, America has $6.2 trillion worth of mineral and metal reserves, but depends on foreign sources for over 50% of the minerals and metals upon which U.S. manufacturers rely.
The authors also remind readers about the Reshoring Initiative’s analysis of hundreds of case studies. “The most important reshoring factor”, they explain, “is proximity.” Shortening the supply chain reduces lead times, freight costs, and excess inventory. Supply chain disruptions are still possible, but less likely. As an NYS manufacturer, how are ensuring that your company can acquire the production materials it needs?
Want more news, updates, and insights about NYS manufacturing? Join the FuzeHub mailing list and begin receiving our free email newsletters.
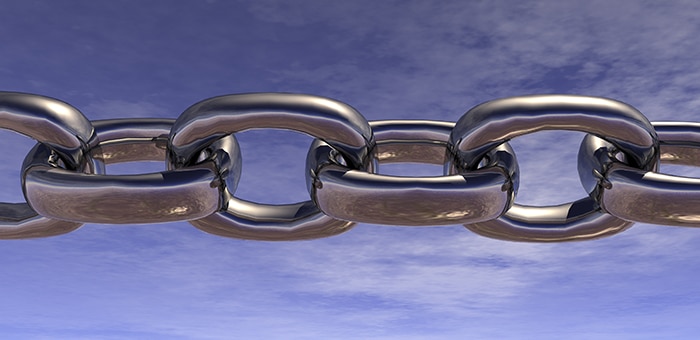